In this article we're going to dive into some examples of clothing quality control errors we've found from well-known brands. Why? To help you understand what's acceptable, and what's not.
We're all guilty of assuming our favourite brands make high quality garments. I mean who buys something and immediately gets the tape measure out to check that the shoulder seams are the same length? Well, actually, we do!
We're not writing this article to tear down any brands, we're doing it to highlight what's commercially viable (allowable) in terms of clothing quality control, so you as a clothing brand owner can take a load of pressure off yourself in comparison to the big brands that are out there!
Garment manufacture is a human-made process, meaning human errors are always going to happen - we're not perfect! Take two t-shirts, made one after the other, same tech pack, same design, same seamstress, same sewing machine. Realistically even these will never be identical! People aren't perfect and garment manufacture will always have variations in it, even if it's just by a tiny amount.
Expecting your manufacturing to come out millimetre-perfect every time is just not realistic, and in this article we're going to dive into some examples of quality errors we've found in some well-known brands pieces.
So, let's take a look at a few defects that we've found recently...
Shoulder seams different measurements
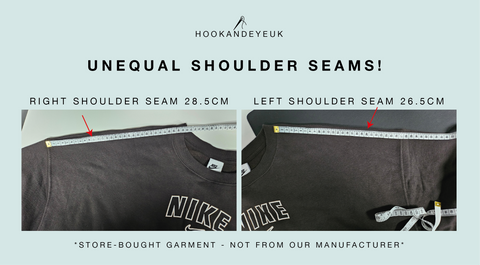
Take a look at this Nike sweatshirt. It might seem fine at a glance but when we got the tape measure out we discovered one shoulder seam is 26.5cm long, and the other shoulder seam 28.5cm long. That's a difference of 2cm!
The clothing industry has 'tolerance' levels set for manufacture, because as mentioned above, items will rarely be completely perfect. The tolerance level tells you what is acceptable, so a seam may be allowed to be up to 1cm off before being rejected, for example. The tolerance level will be agreed with the manufacturer, factoring in fabric, fit, and what is realistically achievable in manufacture.
This Nike sweatshirt could well sit within the tolerance levels on each shoulder, however the outcome is an unsymmetrical garment, so at Hook and Eye UK this wouldn't pass our clothing quality control checks.
Uneven collars
This Lululemon t-shirt has a fabric collar (the band around the neck). You can tell just by looking that it's uneven, and when you compare the side to the centre front, you can see the depth of that collar fluctuates by 0.5cm. It should be the same depth all the way around.
You can also tell that the label hasn't been sewn in to the inside of the collar centrally. This isn't a huge issue as it doesn't affect how the garment looks when worn, it's just another example of human error in the clothes manufacturing process!
Untrimmed threads
This is a really common one and usually not classed as a fault at all. It might bug you if your collection arrives and you find some untrimmed threads on a garment but it's actually completely normal in the manufacturing industry and not classed as a fault.
It's usually just where the ends of the threads have not been cut close enough and doesn't affect the construction of the garment. It only becomes an issue if the stitching comes unravelled when pulled - this shouldn't happen. Take a look at the below examples - t-shirts from Vetements and Palm Angels. You'll see untrimmed threads on the inside and outside.
Uneven hem not caught in
This is to do with hems and how they are finished using a coverstitch. (Take a look at your t-shirts, you'll see two lines of stitching on the outside, and a looped stitch line on the inside - this is a coverstitch). The coverstitching literally 'covers' the raw edge of fabric with this looped stitching.
But as you'll see from the below examples, the raw edge isn't always completely caught in, leaving small areas of excess fabric hanging over. These tees are from Moschino and Vetements - even the big clothing brands have quality control defects!
Quality Control: What's acceptable quality, and where do Acceptable Quality Levels (AQLs) come in to it?
Now to be clear, we're not saying you should accept bad quality just because everyone (even designer clothing brands) has faults. There needs to be a limit to what's commercially viable. It's also important to understand that there is no universal level of quality when it comes to clothing quality control. What's acceptable for some brands will not be acceptable for others. There are, however, ways to measure quality levels...
AQL (Acceptable Quality Level) is the most widely used term for quality levels in the clothing manufacturing industry and it's basically a scoring system that helps control the quality level of a manufacturing run.
The AQL number stipulated by the manufacturer decides the maximum number of defects that are acceptable in a batch of clothing. The scale goes from 0 to 6.5 - the lower the AQL number, the less faults are allowed to pass through, meaning a better overall quality shipment of clothing.
At Hook and Eye UK we manufacture to a quality standard of 1.5, which is significantly better than a lot of low unit clothing manufacturers. Most low MOQ clothing manufacturers only have an AQL of between 2.5 - 4, which means a lot more faults can be accepted when going through the final quality control checks.
How are Acceptable Quality Levels checked in the clothing industry?
A shipment of clothing will be quality checked before it leaves the factory. A percentage of items are picked and assessed against a clothing quality control manual which has a list of categories that must be checked. Any defects are logged and categorised by severity. If the number of faults found exceeds the amount allowed (indicated by the AQL), the full shipment must be inspected and any defective garments rectified or discarded to ensure the AQL is met.
Defects or faults fall into one of three categories, minor, major, or critical, depending on their severity and placement. It's basically a way of deciding how much the defect will affect the saleability and functionality of the garment and therefore whether it's acceptable or not.
Clothing quality control checks are performed manually by factory workers to the guidelines they are given. However, it's a human process, and humans make mistakes! There are some real shockers that can slip through the net - in one of my previous jobs I received a stock sweatshirt from a supplier that had two completely different sized sleeves!
Obviously a mistake by the machinist who had attached the wrong sized sleeve to the wrong body. This is a more extreme example that definitely wouldn't pass a quality control check and should have been caught.
But minor issues like a seam being off by a few millimetres, or there being some untrimmed threads around the stitching, are what's known as commercially viable defects and fall within tolerance levels.
This means basically that it's acceptable, and the garment can still be sold. This isn't manufacturers being lazy, it's taking into account that these items are human-made, will never be perfect, and overall don't affect the finished garment - they're such small defects that you wouldn't notice unless you go looking for them. This is a realistic and more environmentally friendly approach - if garments were rejected and thrown out for not being completely perfect every time there would be no end of wastage.
Why don't all clothing manufacturers work to a high quality level?
Surely, you're thinking, better quality is BETTER, so why don't all clothing manufacturers use the best AQL? It largely comes down to cost. Manufacturing to a higher quality level means more work for the factory; more clothing quality control checks, more defects that have to be rectified or re-made, more time spent. And this equals more cost. Therefore you'll be charged more for your items to be made to a higher quality level.
In Conclusion: What's acceptable in Clothing Quality Control
What you buy isn't perfect! So don't stress about your brand being perfect - even the super fancy big clothing brands have small quality defects - it's inevitable.
Fashion manufacturers work within a tolerance margin - allowing for slight variations on measurements and size.
There is no one level of quality control within the clothing industry - it's all down to the agreement between you and the factory. Improve the quality of your collection by manufacturing to a good Acceptable Quality Level (AQL). Remember, with AQLs, the lower the number the better!).
Any decent clothing manufacturer will make sure your garments go through the quality control process before leaving the factory. But it's advisable to carry out your own checks after bulk manufacture too - check out our guide on how to quality check your garments after bulk manufacture.
You get what you pay for - better quality costs more, so make sure your retail pricing reflects this. (If you want some help with pricing your garments right, check out our article on fashion brand pricing strategy.)
Love, Bethany H&E xx
P.s We're here for you if you have questions drop us a WhatsApp on +447939591255